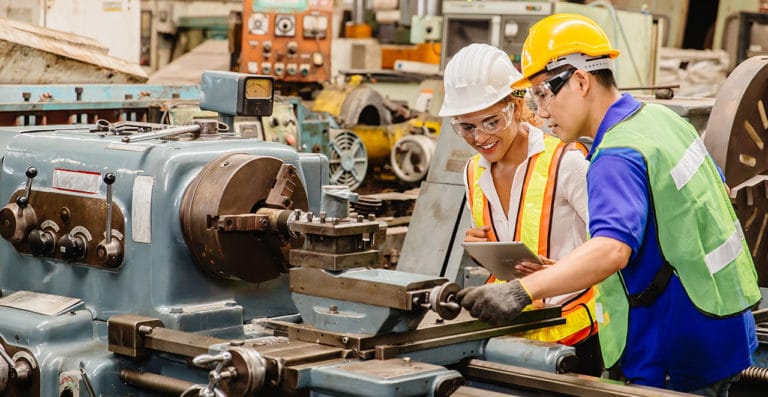
Use a two-pronged approach that couples new recruitment approaches with technology to provide transparent operational insight.
Key Takeaways:
- Supply chain disruptions and labor shortages provide separate yet connected challenges
- Labor shortages are a global problem – contraction has already happened in Germany, Poland, Russia, and Japan and is expected to quicken
- From the top floor to the shop floor, workers are quitting their jobs at a rapid rate
- Supply chain executives must look at new sources for workers and provide the technology that allows the supply chain visibility they need to recruit and retain top talent
- It’s a time of crisis, but out of ashes often comes opportunity; get ready!
Today’s supply chain is challenged by the impact of what would appear to be two disparate challenges: constant supply chain disruptions, and what’s been dubbed “The Great Resignation.” Organizations must use every means at their disposal to keep goods moving while at the same time preventing their most important resource – their talent – from jumping ship at an alarming pace.
Roughly 25% of workers plan to change jobs in 2022. In February alone, 22,000 people in the U.S. resigned from their jobs in durable goods manufacturing. Food supply chains already heavily damaged by the effects of COVID-19 have received yet another blow from labor shortages. The trucking industry was down 80,000 drivers in 2021, and that shortage is anticipated to balloon to 160,000 by 2030.
It’s a global problem. The labor supply is shrinking in Germany, Poland, Russia, and Japan, and contraction is expected to quicken. China, which had a worker surplus of 55.2 million to 75.3 million in 2020, could have a worker shortage of up to 24.5 million by 2030. The overall outlook for supply chains is bleak, leaving executives racking their brains for the key to supply chain resiliency.
It’s time for decisive action. Let’s look at how labor and talent shortages wreak havoc on a supply chain, and the steps leaders can take to solve problems now and protect their organizations in the future.
How Labor and Talent Shortages Affect Supply Chains
There are labor shortages affecting all aspects of the supply chain, from raw materials to final product delivery. The Bureau of Labor Statistics says that, while the manufacturing sector as a whole is projected to have some pandemic recovery employment growth, it also contains 11 of the 20 industries that are predicted to have the most rapid employment declines. These include transportation and material moving, warehouse and fulfillment center workers, truck drivers, call center agents, delivery services, and manufacturing workers.
It’s not just skilled, semi-skilled, and manual labor that’s lacking. Supply chain managers are also leaving, with more mulling over their part in the great resignation. This is all happening while the proliferation of eCommerce has driven up demand for supply chain labor. Then, there’s the Infrastructure Investment and Jobs Act – the construction industry is expected to pull workers from the supply chain since both logistics and construction attract similar worker pools.
Of course, all of this has obvious effects on the supply chain, including:
- A lack of longshoremen and dock workers to unload ships
- Not enough drayage drivers, which means shipping containers sit in ports instead of moving down the chain
- A shortage of long-haul truckers – so shippers can’t move inventory quickly from ports to distribution centers
- Warehouses are understaffed and distribution centers can’t work at full capacity. This results in delays that cause material or inventory shortages that affect both manufacturers and retailers
- Fulfillment centers that are short of workers can’t keep pace with order fulfillment volumes fueled by eCommerce.
And so it goes on, and on, and on. Labor shortages in any of these instances cause issues up and down the supply chain, but combined they have a crippling effect. You’re likely aware of these issues, so let’s move on to what you can do to minimize the effects of labor shortages on supply chain resiliency.
Supply Chain Resiliency in the Face of Labor Shortages: A Two-Pronged Approach
Supply chain executives have two problems here. You have the seemingly uncontrollable supply chain disruptions along with a labor and talent shortage. The remedy is far from simple, but you can greatly reduce the impact of these challenges with advanced technology coupled with talent management strategies.
To ensure you have the workers you need now and in the future, approach your talent pipeline the same way you approach your supply chain:
- Make sure you have complete visibility into your supplier base. Implement a supply chain management platform that easily allows you to find suppliers with large labor forces who can ensure operational viability and find and connect with alternative vendors that can lower first- and second-tier risk.
- Look beyond wages. Competitive wages and attractive benefit packages go far, but take time to examine why workers are leaving your organization and implement fixes. Automate what you can to reduce repetitive work.
- Identify stresses in your supply chain and adjust labor flows. Shift the flow in your supplier network away from those who are labor-stressed. Reroute orders to other warehouses and manufacturing locations. If necessary, change product design or formulations to reduce the need for components and ingredients from labor-strained areas.
- Take a look at your product and services portfolios so you have a deep understanding of each offering and its trade-offs, both operationally and commercially. The goal is to reduce complexity in a way that has a limited impact on sales.
Solving the labor crunch also means exploring new sources of supply. Transition programs for prisoners and veterans’ programs can be good sources of labor. Also, look for workers in industries where employment is declining and reskill them. Connect with local community colleges and technical schools.
Returning to the issue of visibility – because how can you fix something you can’t see? – demand planners play a big role here. A digital supply chain platform can give planners the insight they need to account for different scenarios and facilitate collaboration across the organization to solve current problems and plan for the future.
And for supply chain resiliency even during labor shortages, you need a platform that offers a user-friendly interface along with deep analytics that can attract and retain top planning talent. stichd, a Netherlands-based product licensing company and division of PUMA, recently selected the Logility® Digital Supply Chain Platform to support its ambitious growth strategy and demonstrate investment in its workforce. “Growth is our top priority. To continue achieving our goals, it was critical to find a planning platform with more sophisticated forecasting and clear visibility capabilities, but that is also easy for our employees to use,” said Rogier Wijnhoven, COO at stichd.
Today’s challenges require informed decision-making. You need transparency: real-time data along with artificial intelligence, machine learning, and automation that continually senses, analyzes, and updates activity throughout your entire supply chain. You need granular detail to reach peak operational performance and to prepare for unexpected supply chain events – labor shortages and otherwise.
As John F. Kennedy said, “When written in Chinese, the word ‘crisis’ is composed of two characters – one represents danger and the other represents opportunity.” Be sure you have all the tools you need, both human and digital, to overcome today’s dangers and be poised for tomorrow’s opportunities.
Get the Solutions You Need for True Resiliency with Logility
Logility helps companies accelerate their digital, sustainable supply chain by providing solutions that don’t just present and model data – they drive actionable insights that deliver real and measurable value, so companies can respond to changing market dynamics and more profitably manage their complex global business.
The Logility® Digital Supply Chain Platform leverages an innovative blend of artificial intelligence (AI) and advanced analytics to automate planning, accelerate cycle times, increase precision, improve operating performance, break down business silos, and deliver greater visibility. We help you make smarter decisions faster – reach out to our team to discuss our supply chain solutions.