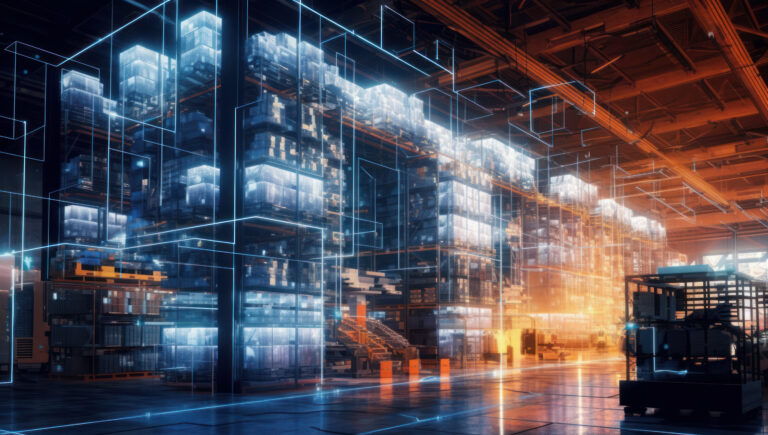
Industrial durables companies face the perpetual challenge of managing items with intermittent demand patterns. These items often exhibit sporadic and unpredictable fluctuations in demand, making traditional inventory management methods less effective. To tackle this issue, many industrial durable companies are turning to probabilistic inventory planning, a data-driven approach that offers practical solutions to the unique challenges of managing intermittent demand. Let’s define what probabilistic inventory planning is and explore why companies should embrace this approach.
What is Probabilistic Inventory Planning?
Probabilistic inventory planning is an advanced inventory management methodology that incorporates randomness and uncertainty into the decision-making process for items with intermittent demand patterns. It leverages stochastic processes and simulations to make informed decisions about when and how much to reorder. Unlike deterministic inventory models, stochastic replenishment planning acknowledges and quantifies the inherent variability and unpredictability in demand.
Probabilistic Forecasting:
Probabilistic (or stochastic) forecasting is a method that involves incorporating randomness or stochastic processes into models to generate forecasts. Probabilistic forecasting recognizes that various factors contributing to a forecast may have inherent uncertainty or variability, and it models this uncertainty by introducing randomness into the forecasting process. The key characteristics of Probabilistic forecasting are:
- Utilizes random variables or stochastic processes to represent uncertainty.
- Often used in simulations, Monte Carlo simulations, or Markov processes.
- Allows for the exploration of different possible outcomes through repeated random sampling.
- Suitable for modeling complex systems with inherent variability.
For example, in financial modeling, probabilistic forecasting might be used to simulate stock price movements over time, considering the random nature of market fluctuations. This approach generates a range of potential future price scenarios based on historical data and assumed stochastic processes.
Key Components of Probabilistic Inventory Planning:
Stochastic Models: Probabilistic Inventory planning utilizes probabilistic or stochastic models to represent the demand patterns. These models account for the randomness and variability in demand, allowing for more accurate forecasting and decision-making.
Monte Carlo Simulations: Probabilistic inventory planning often employs Monte Carlo simulations, a computational technique that generates multiple possible demand scenarios by repeatedly sampling from probability distributions. This enables companies to assess the range of possible outcomes and their associated risks.
Reorder Point and Order Quantity: Unlike deterministic methods that rely on fixed reorder points and order quantities, probabilistic inventory planning calculates these parameters probabilistically. It considers not only the average demand but also the entire distribution of potential demand values.
InventoryAI+: Transforming Chaos into Triumph
Watch this dynamic webinar to learn more about the cutting-edge solution designed to revolutionize the way supply chain professionals optimize inventory and maximize performance.
OnDemand WebinarWhy Should Industrial Durable Companies Use Probabilistic Inventory Planning for Intermittent Demand?
Embracing Uncertainty
Intermittent demand items in the industrial durable sector are notorious for their unpredictable and sporadic fluctuations. Traditional inventory management methods often struggle to handle this inherent uncertainty, leading to either frequent stockouts or overstocking. Probabilistic inventory planning addresses this challenge by embracing uncertainty, modeling it, and factoring it into the decision-making process.
By incorporating probabilistic (or stochastic) processes and simulations, industrial durable companies can explore the various ways in which demand can unfold. This approach provides a more comprehensive understanding of the potential outcomes, enabling companies to make more informed and robust inventory decisions.
Accurate Forecasting
One of the primary advantages of probabilistic inventory planning is its ability to generate more accurate demand forecasts. Instead of relying on point estimates, this approach provides a range of possible outcomes, along with their associated probabilities. This enhanced forecasting accuracy allows industrial durable companies to better align their inventory levels with actual demand patterns, reducing the likelihood of stockouts or excess inventory.
For instance, a company that manufactures heavy machinery components may experience intermittent demand due to variations in construction projects. Probabilistic inventory planning helps this company generate a distribution of possible demand values, which are far more informative and reliable than a single-point estimate, ensuring that they maintain optimal inventory levels for each component.
Reduced Holding Costs
Holding costs are a significant concern for industrial durable companies. These costs encompass expenses such as warehousing, insurance, depreciation, and opportunity costs associated with inventory holding. When dealing with items exhibiting intermittent demand, the risk of holding excessive inventory is substantial.
Probabilistic inventory planning mitigates this risk by using probabilistic approaches to calculate optimal inventory levels. By considering the variability and randomness in demand, this approach ensures that safety stock levels are adequate to handle fluctuations, reducing the need for excessive inventory. As a result, industrial durable companies can significantly reduce holding costs, leading to improved profitability.
Minimizing Stockouts
Stockouts can lead to production delays and customer dissatisfaction in the industrial durable sector, where timely deliveries and project schedules are crucial. Probabilistic inventory planning is designed to minimize stockouts by considering the entire distribution of potential demand outcomes. This approach ensures there is a sufficient buffer of safety stock to handle unexpected demand spikes.
Consider a company that manufactures custom equipment for specialized industrial applications. Some components may exhibit intermittent demand patterns due to variations in custom orders. Probabilistic inventory planning helps the company calculate safety stock levels that are responsive to the inherent variability in demand, ensuring that customers receive the components they need on time and preventing production delays.
Efficient Resource Allocation
Probabilistic inventory planning aids industrial durable companies in efficiently allocating their resources. By accounting for uncertainty and modeling demand variations, companies can optimize their purchasing and production processes. This means they can strategically allocate resources, such as labor and raw materials, to match the expected demand scenarios more effectively.
For example, a company manufacturing custom steel structures may experience intermittent demand for various types of steel. Probabilistic inventory planning can help this company make informed decisions about when to order specific steel types and in what quantities, ensuring that resources are used efficiently and avoiding unnecessary idle capacity.
In the industrial durable sector, where intermittent demand and project-based manufacturing are common, probabilistic inventory planning offers a powerful tool to address inventory management challenges effectively. This approach embraces uncertainty, provides more accurate forecasting, reduces holding costs, minimizes stockouts, and optimizes resource allocation. Companies that implement probabilistic inventory planning can achieve enhanced forecasting accuracy, cost savings, and improved customer satisfaction.
Making the right decisions regarding inventory management is crucial. For companies dealing with intermittent demand items, probabilistic inventory planning offers a data-driven and practical solution to the persistent challenges of inventory optimization. By embracing stochastic processes and simulations, companies can unlock the full potential of their inventory management processes, leading to greater efficiency, profitability, and customer satisfaction in the industrial durable sector.
Written by
Lachelle Buchanan
Vice President, Product Marketing
Short bio
Lachelle Buchanan is the vice president of product marketing at Logility, where she leverages over 15 years of experience in unifying the expertise of product development teams with the market insight of sales teams for successful new product introductions. After spending half her career in marketing and the other half in supply chain, Lachelle is most passionate about bringing teams together to solve complex supply chain challenges and delivering value for customers. Owing to a passion for advanced Sales & Operations Planning, Lachelle has Oliver Wight certifications in Integrated Business Planning (Advanced S&OP), Demand Management, Integrated Supply Chain Management and Product & Portfolio Management.